فرایند تولید ناودانی
- اسفند 1, 1403
- 12:00 ب.ظ
- بدون دیدگاه
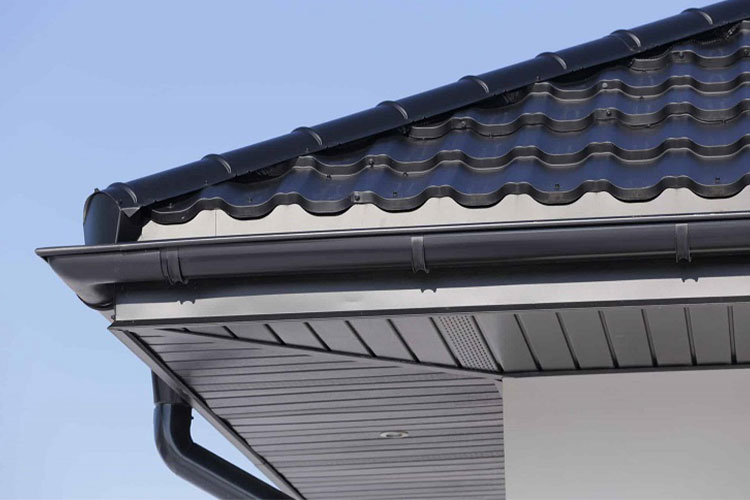
روش تولید ناودانی و نبشی شباهت زیادی به هم دارد و هر دو آنها با دو روش پرسی و فابریک تولید میشوند. همچنین نحوه ساخت و تولید نبشی و ناودانی تفاوتی با هم نداشته و تنها در فرمدهی و محصول نهایی با هم متفاوت هستند. در این مطلب قصد داریم به نحوه تولید ناودانی پرداخته و شما را با فرمولهای ساخت آن آشنا کنیم. لازم به ذکر است که بعضی از اشکال ناودانی تنها با روشی مخصوص تولید میشود؛ بنابراین آشنایی با دستهبندی ناودانی قبل از بررسی روشهای تولید آن ضروری است.
به طور کلی میتوان گفت که ناودانیها بر اساس وزن و شکل دستهبندی شدهاند. ناودانیهای سبک دارای بالهای کاملاً موازی و همینطور ضخامت یکسان هستند؛ زیرا وزن این ناودانیها از وزن استاندارد جدول اشتال سبکتر است. همچنین این ناودانی به دلیل تفاوتهایی که در زاویه گوشههای آنها وجود دارد، در دو نوع U و C دستهبندی میشود. ناودانی سنگین یا ناودانی اروپایی نیز دارای بالهایی است که با دور شدن از جای آن کاهش خواهد یافت. این ناودانی دارای وزن استاندارد جدول اشتال است.
برای دریافت قیمت ناودانی و مشاوره رایگان با کارشناسان ما تماس بگیرید.
فرمول سازی تولید ناودانی
لازم است بدانید که تولید ناودانی از قرن بیستم انجام شده و در ابتدا در ساختمانسازی مورد استفاده قرار میگرفت. با گسترش صنایع گوناگون، سفارش ناودانی و به طور کلی محصولات فولادی افزایش پیدا کرد. به همین علت نیز تولید قطعات فولادی افزایش یافت.
ناودانی نوعی پروفیل محسوب شده که به شکل حرف انگلیسی U است. این قطعه دو بال و یک جان دارد. بخشهای عمودی ناودانی بالها بوده و قطعه فلزی افقی آن نیز جان است. در صورتی که بالهای ناودانی به شکل موازی باشند، ناودانی موازی نامگذاری شده و چنانچه غیرموازی باشند، به آن ناودانی شیبدار میگویند. به علاوه ناودانیها در انواع و اقسام سبک و سنگین و همچنین ساده و مشبک تولید میشوند.
مثل گذشته بهبود طراحی غلتک نیاز به تحقیقات در حوزه فلزی دارد. از طرفی خیلی از ابهاماتی که در ارتباط با رفتار فلز در کالیبرهای گوناگون وجود دارد، بررسی نشده و مطالعات آزمایشی نیز هزینه زیادی را در بر میگیرد. به همین دلیل از فناوریهای رایانهای در آزمایشات دشوار استفاده میشود تا امکان بررسی آزمایشات پیچیده و پروندهها مقدور شود.
ناودانیها از لحاظ شکل ظاهری نیز به چند دسته تقسیم میشوند. آشنایی با انواع آنها میتواند تأثیر زیادی در اطلاع از فرآیند تولیدشان داشته باشد. ناودانی ساده در سایزها و ابعاد مختلفی با توجه به درخواست مشتری تولید میشود. ناودانی ساده کاربرد زیادی در صنایع مختلف داشته و از آن در ساخت اتاق ماشینهای سنگین و چهارچوبها استفاده میشود.
فرایند تولید ناودانی چگونه است؟
باید بگوییم که از دو روش اصلی برای ساخت قسمتهای ناودانی در نورد استفاده میشود که نبرد با بالههای مستقیم و نبرد با بالههای باز نشده نام دارد. در صورتی که بالهها خم شوند، میتوان از طراحی غلتک با بالههای باز نشده کمک گرفت. رشد شیب باله میتواند مصرف برق را کاهش دهد و منجر به افزایش دوام غلتکها شود.
به طور تقریبی میتوان گفت که تمامی انواع ناودانیها به روش فابریک تولید میشوند. این روش همان روش نورد گرم بوده که خیلی از مقاطع فولادی نیز با همین شیوه تولید میشوند. در فرآیند تولید ناودانی فابریک فشار کمتری در مقایسه با فرآیند تولید تیرآهن وارد میشود و شکلدهی بال ناودانی صورت میگیرد.
روشهای تولید ناودانی
ناودانی فابریک در دو روش عمده تولید میشود که مرحله مشترک در هر دو آنها به کارگیری شمش فولادی و حرارت دادن آن خواهد بود. تولید ناودانی به روش اول با استفاده از چند غلتک انجام شده و شمش فولادی را در کورهای گرم میکنند تا با عبور از بین غلتکها باریکتر شود و به شکل ناودانی دربیاید.
در روش دوم، شمش حرارت داده شده را با چند ضربه به صورت ناودانی تغییر میدهند و از قالب سرد استفاده میکنند. خط تولید این ناودانیها، یعنی ناودانی مشبک و ناودانی گالوانیزه یک مرحله بیشتر هم داشته که در این مرحله روند تولید بیشتر بوده و به شکل سرد در دمای اتاق انجام میشود. ساخت ناودانی فابریک از کیفیت بالایی برخوردار است.
ناودانی مشبک نیز به طور گسترده در صنعت مورد استفاده قرار میگیرد. در تولید این ناودانی سوراخهای شبکهای وجود داشته که موجب کاهش وزن ناودانی میشود. البته این مورد از استحکام این محصول چیزی کم نکرده است؛ بنابراین برای ساختن قفسههای مقاوم از ناودانیهای مشبک استفاده میکنند تا ضمن برخورداری از استحکام، وزن پایینی داشته باشند.
به طور معمول میتوان گفت که ناودانیهای مشبک از جنس ورق گالوانیزه بوده و به دو صورت گرم و سرد تولید میشوند. وجود سوراخهایی در بدنه قطعه و همینطور شکل ظاهری در این ناودانیها باعث تفاوت آنها با ناودانیهای ساده شده است.
روش نورد برای ایجاد یک شبکه خمیده و شیب در باله مورد استفاده قرار گرفته و باید در مرحله آخر آن از یک ایستگاه غلتک زنی استفاده شود. هنگامی که ایستگاه نورد استاندارد به صورت خمشی عمل میکند، موجب کاهش بار در طول نورد با پایهای ثابت شده و مزایای بسیاری به همراه دارد.
با این حال بهترین طرح مسیر نورد روباز بوده که روند خوبی را در قسمتهای ناودانی کوچک و متوسط از خود ارائه میدهد. روش خمشی در نورد از طراحی پیشرفتهای برخوردار است که باعث کاهش یکنواخت بودن ضخامت ناودان و همینطور ایجاد عمق کم و ابعاد کمتر خواهد شد. البته این روش معایبی مانند خم شدن دیوارههای ناودانی نیز دارد؛ زیرا در این صورت امکان وجود خسارت در سطح بالهها نیز به وجود خواهد آمد.
نحوه تولید ناودانی فابریک گرم و سرد
تولید ناودانی فابریک به روش سرد مشابه تولید نبشی و قوطی پروفیل بوده که ماده اولیه در خط تولید آن ورق سیاه است. از طرفی ضخامت ورق سیاه در تمامی نقاط یکسان است و به همین علت نیز در این روش امکان تولید ناودانی UNP وجود نخواهد داشت. در روند تولید ناودانی پرسی نقش اصلی را دستگاه پرس ایفا کرده و اخیراً به کارگیری دستگاه رول فرمینگ نیز در این روش رایج شده است.
در تولید این محصول به روش سرد، در ابتدا ورق فولادی به صورت نوار بریده شده و ابعاد آن برابر با مجموع عرض بالهای ناودانی است. در ادامه نوارهای ورق به دستگاه رول فلمینگ وارد شده و با اعمال فشاری که توسط غلتکها صورت میگیرد به شکل ناودانی درمیآید.
لازم به ذکر است که روش تولید ناودانی در کیفیت آن موثر است. در روش نورد گرم نیز شمشهای فلزی حرارت دیده و از غلتکهای عمودی و افقی عبور میکنند و به صورت ناودانی درمیآیند. در نهایت نیز میتوان آنها را در ابعاد دلخواه برش داد. ناودانیهایی که به این روش تولید میشوند، فرصت لازم را برای انجام فرآیند در اختیار ندارند.
در زمان طراحی مسیر نورد توصیه میشود که از مسیرهای کنترلکننده استفاده کنید؛ زیرا در این صورت ارتفاع اولیه شمش افزایش خواهد یافت. به طور معمول در طرحهای گوناگون از یک یا دو مسیر تست استفاده شده که یکی از آنها مسیر مقدماتی و دیگری مسیر پرفشار نام دارد.
سخن پایانی
با توجه به موارد گفته شده، در مییابیم که نحوه تولید ناودانی تعیینکننده کیفیت آن است. از طرفی اطلاع از نحوه تولید و ساخت ناودانی و همینطور فرآیند تولید آن باعث میشود تا بتوانید از صحت هر ادعایی در ارتباط با کیفیت ناودانی مورد نظر خود اطمینان حاصل کنید. لازم به ذکر است که قیمت بالای این محصول هرگز به معنای کیفیت بالای آن نیست. در نتیجه در زمان خرید ناودانی لازم است تا عوامل مختلفی را در نظر بگیرید و نوسانات قیمت آهن را نیز در نظر داشته باشید. پیشنهاد می کنیم برای اطلاع از قیمت روز میلگرد به سایت مهراستیل مراجعه کنید.
سوالات متداول
تولید ناودانی به روش پرسی چیست؟
در روش پرسی دستگاه رول فرمینگ یا پرس، جهت شکلدهی به ورقهای فولادی و تغییر آنها به ناودانی مورد استفاده قرار میگیرند.
تولید ناودانی به روش فابریک به چه صورت است؟
این روش مانند تولید تیرآهن است و با چند پرس انجام میشود.
تولید ناودانی سنگین به چند روش صورت میگیرد؟
این روش با سه روش نورد گرم، سرد و فابریک انجام میشود.
کاربرد ناودانی سنگین چیست؟
این ناودانیها در بندها و در ستونها مورد استفاده قرار میگیرد.
در زمان خرید ناودانی بایستی به چه نکاتی توجه شود؟
استاندارد ساخت، شکل ظاهری و همینطور قیمت روز این مقاطع از مواردی است که در زمان خرید ناودانی باید مورد توجه قرار بگیرد.
مقالات پربازدید
- تکنولوژی جوش ERW در لولههای داربستی: چگونه خط جوش ناپیدا ایمنی را تضمین میکند؟
- تحلیل هزینه چرخه عمر (LCCA) لوله داربستی باکیفیت: چرا سرمایهگذاری اولیه بهصرفه است؟
- بررسی علل شکست لولههای داربستی در سایتهای ساختمانی: درسهایی از حوادث واقعی
- اصول ایمنی داربستبندی بر اساس نوع لوله: چرا قطر ۴۸.۳ میلیمتر استاندارد طلایی است؟
- کاربرد لولههای گازرسانی خانگی