نگهداری و افزایش عمر لولههای داربستی: ۷ راهکار عملی پس از گالوانیزاسیون
- تیر 12, 1404
- 9:26 ق.ظ
- بدون دیدگاه
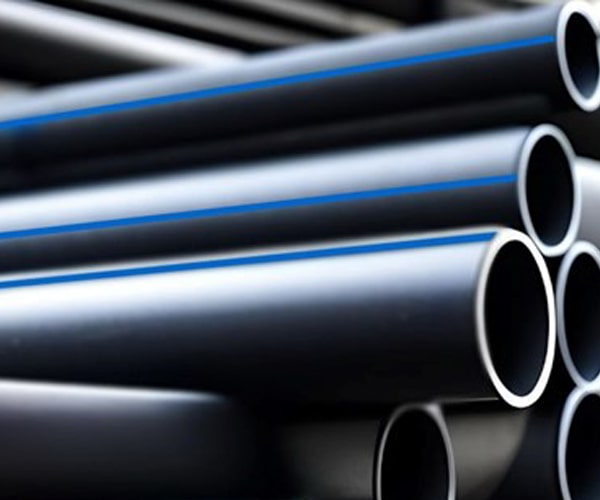
مقدمه :
لولههای داربستی، ستون فقرات پروژههای ساختمانی و صنعتی هستند که ایمنی کارگران و موفقیت عملیات را تعیین میکنند. کیفیت این لولهها تنها به ظاهر آنها محدود نمیشود، بلکه مجموعهای پیچیده از عوامل مواد اولیه، فرآیند تولید، کنترل کیفیت و استانداردها را در بر میگیرد. شرکت فولاد مهر سهند، به عنوان تولیدکننده پیشرو در زمینه مقاطع فولادی از جمله لولههای صنعتی و داربستی به روش فورمینگ و نورد سرد، اهمیت ویژهای به رعایت این عوامل حیاتی میدهد. درک این عوامل برای انتخاب لولههای داربستی مطمئن و با طول عمر بالا ضروری است.
لوله های داخل تراشی شده تولید شده به روش جوش درزدار: دقت بالا برای کاربردهای حیاتی
۱. کیفیت مواد اولیه: سنگ بنای استحکام
* گرید فولاد: استفاده از فولادهای ساختمانی مرغوب با گریدهای استاندارد مانند ST37 (مطابق استاندارد ملی ایران) یا معادل بینالمللی آن مانند S235JR/S235J0 (طبق استاندارد اروپایی EN) و A53 Gr.B (طبق استاندارد آمریکایی ASTM) ضروری است. این گریدها ترکیب شیمیایی بهینه (کربن، منگنز، سیلیسیوم، فسفر، گوگرد) و خواص مکانیکی پایه (استحکام کششی و تسلیم) مناسب برای تحمل بارهای وارده را تضمین میکنند.
* کویل/ورق فولادی: کیفیت سطح، یکنواختی ضخامت در طول کویل و عدم وجود عیوب سطحی (مانند پوستهپوستهشدگی، ترک یا ناخالصیهای فراوان) در مواد اولیه ورودی به خط تولید، مستقیماً بر کیفیت نهایی لوله تاثیرگذار است.
* کنترل ترکیب شیمیایی: آزمایشهای اسپکترومتری برای اطمینان از انطباق ترکیب شیمیایی فولاد با استاندارد مورد نظر، اولین قدم در تضمین خواص نهایی است.
۲. فرآیند تولید: شکلدهی و اتصال
* روش تولید: لولههای داربستی معمولاً به روش جوش مقاومتی الکتریکی (ERW) تولید میشوند. کیفیت جوش درز لوله، مهمترین عامل در استحکام و ایمنی آن است.
* تنظیمات دقیق جوش: پارامترهای جوش (جریان، ولتاژ، سرعت، زاویه الکترود، فشار غلتکها) باید به دقت کنترل شوند تا نفوذ کامل جوش حاصل شده و عیوبی مانند عدم نفوذ (Lack of Penetration)، تخلخل (Porosity) یا ترکهای ریز (Micro-cracks) در منطقه جوش ایجاد نشود.
* کیفیت لبهها: لبههای نوار فولادی قبل از جوش باید کاملاً تمیز، صاف و عاری از اکسید، روغن یا آلودگی باشد تا جوش یکنواخت و مستحکم تشکیل شود.
* فرمینگ دقیق: فرآیند شکلدهی نوار به لوله توسط غلتکهای فرمینگ باید با دقت بالا انجام شود. عدم هممحوری، بیضیشدگی (Ovality) یا انحنای نامنظم در طول لوله، نه تنها بر ظاهر، بلکه بر استحکام و قابلیت اتصال لولهها تاثیر منفی میگذارد.
* برداشتن برجستگی جوش (Flash Removal): پس از جوش، برجستگی ایجاد شده در داخل و خارج درز جوش باید به طور کامل و یکنواخت برداشته شود. باقی ماندن برجستگی باعث ایجاد تمرکز تنش و کاهش استحکام خستگی لوله میشود. همچنین، برجستگی داخلی مانع از حرکت آزادانه اتصالات (مثل پینها) در داخل لوله میشود.
۳. عملیات حرارتی و کنترل تنش
* نرمالایزینگ (Normalizing): برای لولههای داربستی که معمولاً از فولادهای کمکربن تولید میشوند، عملیات نرمالایزینگ پس از جوشکاری بسیار رایج و حیاتی است. این عملیات شامل گرم کردن لوله تا دمای مشخص (بالای دمای بحرانی) و سپس سرد کردن در هوای آرام است.
فواید آن شامل:
* ریزبافتتر و یکنواختتر کردن ساختار فلز در منطقه جوش و فلز پایه.
* رفع تنشهای پسماند (Residual Stresses) ناشی از فرآیندهای فرمینگ و جوشکاری که میتوانند باعث تغییر شکل یا ترک خوردگی زودرس شوند.
* بهبود خواص مکانیکی مانند استحکام و چقرمگی.
* کنترل دمای عملیات: دما و زمان ماند در کوره و همچنین سرعت سرد کردن باید دقیقاً کنترل شوند تا نتایج مطلوب حاصل گردد.
۴. گالوانیزاسیون: سپر محافظ در برابر خوردگی
* روش گالوانیزه: لولههای داربستی به دلیل استفاده در محیطهای باز و اغلب مرطوب و خورنده (ساختمانسازی، صنایع دریایی، مناطق با آلودگی بالا) حتماً باید گالوانیزه گرم (Hot-Dip Galvanized) شوند. کیفیت گالوانیزه تاثیر مستقیمی بر طول عمر لوله دارد.
* ضخامت پوشش: پوشش روی باید دارای ضخامت کافی و یکنواخت (معمولاً حداقل ۸۵ میکرون مطابق استانداردهای رایج داربست مانند BS 1139) باشد تا محافظت بلندمدت را تضمین کند.
* آمادهسازی سطح (Surface Preparation): مرحله اسیدشویی (Pickling) و فلوکسزنی (Fluxing) قبل از غوطهوری در روی مذاب، بسیار حیاتی است. سطح لوله باید کاملاً عاری از زنگزدگی، اکسید، روغن و هرگونه آلودگی باشد تا چسبندگی پوشش روی به فولاد (اتحاد متالورژیکی) به بهترین شکل انجام شود.
مقالات پربازدید
- تفاوت بین پروفیلهای زد، سی و یو در سازههای فلزی: راهنمای انتخاب مقطع مناسب برای پروژهها
- استاندارد ملی 7335 ایران در تولید زد سوله: راهنمای انتخاب محصول با کیفیت
- زد سوله چیست و چه نقشی در سازههای صنعتی دارد؟
- فناوریهای نوین در تولید قوطیهای مربع فولادی شرکت فولاد مهر سهند: بهبود کیفیت و افزایش بهرهوری
- بررسی کاربردهای تخصصی قوطیهای مربع فولادی در صنایع مختلف با تمرکز بر محصولات فولاد مهر سهند