عوامل مؤثر بر کیفیت لوله گاز
- تیر 17, 1404
- 12:54 ب.ظ
- بدون دیدگاه
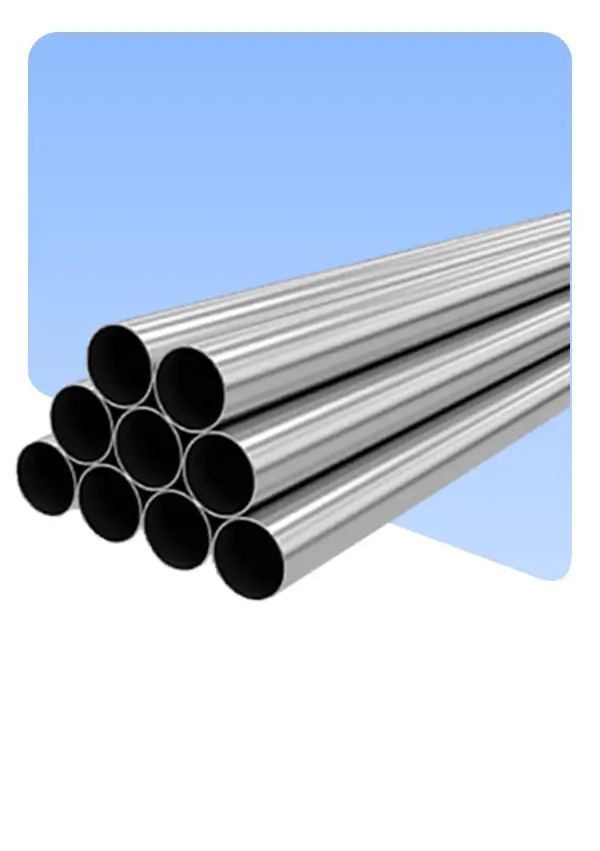
فهرست محتوا
“بررسی تخصصی و فنی توسط شرکت فولاد مهر سهند – تولیدکننده انواع لوله و پروفیل فولادی”
مقدمه
لوله گاز یکی از حساسترین و حیاتیترین محصولات فولادی در صنایع مختلف، بهویژه در بخش انتقال انرژی و سوختهای فسیلی به شمار میرود. کیفیت لوله گاز نهتنها تضمینکننده ایمنی شبکه توزیع گاز است، بلکه مستقیماً بر دوام، کارایی و بهرهوری سیستمهای گازی تأثیر میگذارد. شرکت فولاد مهر سهند به عنوان یکی از برترین تولیدکنندگان لوله و پروفیل فولادی در کشور، همواره بر تولید محصولات باکیفیت و استاندارد تأکید داشته و در این مقاله به بررسی دقیق عوامل مؤثر بر کیفیت لوله گاز میپردازد.
۱. مواد اولیه و ترکیب شیمیایی فولاد
نقطه آغاز کیفیت در هر فرآیند تولید، مواد اولیه است. در تولید لوله گاز، انتخاب فولاد مناسب از نظر ترکیب شیمیایی و خواص مکانیکی، نقشی اساسی در تضمین کیفیت نهایی دارد.
•ترکیب شیمیایی مناسب: درصد کربن، منگنز، گوگرد، فسفر، سیلیسیوم و عناصر میکروآلیاژی باید در محدوده مشخصی باشند تا تعادل میان سختی، انعطافپذیری و مقاومت در برابر خوردگی ایجاد شود.
•کنترل ناخالصیها: حضور عناصر مضری مانند گوگرد و فسفر در مقادیر بالا، موجب شکنندگی و کاهش قابلیت جوشپذیری لولهها میشود.
•استفاده از فولادهای استاندارد: فولادهای مناسب برای لولههای گاز معمولاً طبق استانداردهای بینالمللی مانند API 5L، ASTM A106 یا DIN 2448 تولید میشوند.
۲. فرآیند شکلدهی (Forming)
روش شکلدهی لوله از ورق فولادی (معمولاً به روش نورد سرد یا گرم)، تأثیر مستقیم بر استحکام و یکنواختی دیواره لوله دارد.
•نورد دقیق: در مرحله شکلدهی، یکنواختی ضخامت و قطر لوله اهمیت زیادی دارد. تفاوتهای جزئی در ابعاد، موجب افت فشار یا نشتی گاز در سیستم میشود.
•عدم وجود ترک یا چینخوردگی: در حین خمکاری یا شکلدهی، بروز ترکهای سطحی یا عیوب ساختاری میتواند زمینهساز نقاط ضعف در لوله گاز شود.
•تنشزدایی در حین شکلدهی: تنشهای داخلی که در حین شکلدادن ایجاد میشوند، در صورت عدم کنترل، باعث کاهش طول عمر لوله خواهند شد.
۳. کیفیت جوشکاری
بسیاری از لولههای گاز به صورت درزجوش (Welded Pipe) تولید میشوند و کیفیت نهایی محصول بهطور مستقیم به جوش ایجاد شده وابسته است.
•روش جوشکاری مناسب: معمولاً از جوش مقاومت الکتریکی (ERW) برای تولید لولههای گاز استفاده میشود که نیازمند تجهیزات دقیق و کنترل شده است.
•بررسی کیفیت جوش: استفاده از روشهای آزمون غیرمخرب (NDT) مانند التراسونیک یا رادیوگرافی برای اطمینان از سلامت جوش الزامی است.
•همترازی دقیق لبهها: در مرحله قبل از جوشکاری، باید دو لبه ورق بهطور کامل با یکدیگر تراز شوند تا از تشکیل ناخالصی یا ضعف در ناحیه جوش جلوگیری شود.
۴. آزمونهای کنترل کیفیت (QC)
پس از تولید، لولهها باید از فیلتر دقیق آزمونهای کنترل کیفی عبور کنند تا مناسب بودن آنها برای مصارف گازی تأیید گردد.
•آزمون فشار هیدرواستاتیک: این آزمون برای بررسی تحمل لوله در برابر فشار داخلی انجام میشود. لوله باید بدون نشتی، تغییر شکل یا ترک این مرحله را پشت سر بگذارد.
•آزمونهای مکانیکی: آزمون کشش، خمش، و ضربه برای سنجش خواص مکانیکی مانند استحکام تسلیم، استحکام کششی و چقرمگی فلز انجام میشود.
•آزمون خوردگی: در محیطهای خورنده یا مرطوب، مقاومت لوله در برابر خوردگی اهمیت زیادی دارد، بهویژه اگر از فولاد بدون پوشش استفاده شده باشد.
۵. پوششدهی و محافظت سطحی
در برخی موارد، برای افزایش طول عمر و مقاومت در برابر عوامل محیطی، لولهها با پوششهای خاصی پوشانده میشوند.
•پوششهای ضد خوردگی: نظیر اپوکسی، پلیاتیلن، گالوانیزه گرم یا انواع پوششهای پلیمری، که مانع تماس مستقیم لوله با عوامل خورنده میشوند.
•پوششهای داخلی: برای عبور بهتر جریان گاز و کاهش افت فشار، برخی لولهها دارای پوشش داخلی صاف و مقاوم در برابر اصطکاک هستند.
•نظافت سطحی پیش از پوششدهی: آمادهسازی صحیح سطح لوله شامل سندبلاست، چربیزدایی و خشککردن، نقش کلیدی در چسبندگی و دوام پوشش دارد.
۶. استانداردها و گواهینامههای بینالمللی
رعایت استانداردهای معتبر بینالمللی در تولید لولههای گاز، تضمینکننده ایمنی و قابلیت اطمینان در شبکههای گازرسانی است.
•استاندارد API 5L: یکی از پرکاربردترین استانداردها برای لولههای انتقال گاز و نفت، که بر اساس خواص مکانیکی، ترکیب شیمیایی، و روشهای آزمون تنظیم شده است.
•گواهی ISO 9001: سیستم مدیریت کیفیت جامع در فرآیند تولید که نشاندهنده رعایت کنترل کیفیت در تمامی مراحل تولید است.
•استانداردهای ملی: در ایران، رعایت الزامات سازمان استاندارد و شرکت ملی گاز ایران نیز الزامی است و هرگونه انحراف از این دستورالعملها ممکن است خطرات جدی به همراه داشته باشد.
۷. دقت در حملونقل و نگهداری
لولههایی که برای انتقال گاز تولید میشوند، باید با دقت بالا جابجا و انبار شوند تا دچار آسیب فیزیکی نشوند.
•جلوگیری از ضربه: ضربه یا سقوط لوله در حین بارگیری میتواند موجب ایجاد ترکهای میکروسکوپی و کاهش ایمنی شود.
•انبارداری استاندارد: لولهها باید در محل خشک و دور از رطوبت انبار شوند تا از زنگزدگی و آسیبهای سطحی جلوگیری شود.
•بستهبندی صحیح: استفاده از پلاگ، درپوش و لفاف مناسب، از آلودگی و ورود اجسام خارجی به داخل لوله جلوگیری میکند.
۸. تخصص و مهارت نیروی انسانی
نقش اپراتورها، مهندسان تولید و کارشناسان کنترل کیفیت در تضمین کیفیت نهایی غیرقابل انکار است.
•آموزش مستمر: پرسنل باید با جدیدترین استانداردها، روشهای آزمون و دستگاههای مدرن آشنا باشند.
•تجربه عملی: شناخت کامل از فرآیندهای تولید و نگهداری ماشینآلات موجب افزایش بازدهی و کاهش خطاهای انسانی میشود.
•تعهد به کیفیت: فرهنگ سازمانی مبتنی بر کیفیت، باعث کاهش ضایعات و افزایش بهرهوری کلی سیستم تولید میشود.
۹. تکنولوژی و نوآوری در تولید
استفاده از تجهیزات پیشرفته و فناوری روز، در بهبود کیفیت و افزایش دقت تولید لوله گاز تأثیر بسزایی دارد.
•استفاده از دستگاههای اتوماتیک جوش و بازرسی: کاهش خطای انسانی و افزایش سرعت تولید.
•خطوط تولید پیوسته (Continuous): حفظ یکنواختی در خواص محصول در مقیاس انبوه.
•مانیتورینگ لحظهای: کنترل دقیق ضخامت، قطر، سرعت تولید و دمای جوشکاری به صورت آنلاین.
جمعبندی و نتیجهگیری
کیفیت لوله گاز حاصل ترکیب دقیقی از مواد اولیه مناسب، فرآیندهای تولید کنترلشده، آزمونهای استاندارد، و نظارت مستمر است. هرگونه نقص یا اهمال در هر یک از این مراحل میتواند موجب بروز حوادث، نشت گاز، کاهش عمر مفید سیستم و تحمیل هزینههای سنگین به پروژهها شود.
شرکت فولاد مهر سهند، با اتکا به تجربه چندین ساله در صنعت فولاد و بهرهگیری از تکنولوژی پیشرفته، تیم متخصص و رعایت دقیق استانداردهای ملی و بینالمللی، مفتخر است که جزو تأمینکنندگان اصلی لولههای گازی باکیفیت در کشور محسوب میشود. ما همواره بر آنیم تا با ارتقای کیفیت محصولات خود، گامی مؤثر در تأمین ایمنی، پایداری و توسعه زیرساختهای انرژی کشور برداریم.
مقالات پربازدید
- تفاوت بین پروفیلهای زد، سی و یو در سازههای فلزی: راهنمای انتخاب مقطع مناسب برای پروژهها
- استاندارد ملی 7335 ایران در تولید زد سوله: راهنمای انتخاب محصول با کیفیت
- زد سوله چیست و چه نقشی در سازههای صنعتی دارد؟
- فناوریهای نوین در تولید قوطیهای مربع فولادی شرکت فولاد مهر سهند: بهبود کیفیت و افزایش بهرهوری
- بررسی کاربردهای تخصصی قوطیهای مربع فولادی در صنایع مختلف با تمرکز بر محصولات فولاد مهر سهند