فولادهای زنگ نزن آستنیتی
- دی 17, 1401
- 3:16 ب.ظ
- بدون دیدگاه
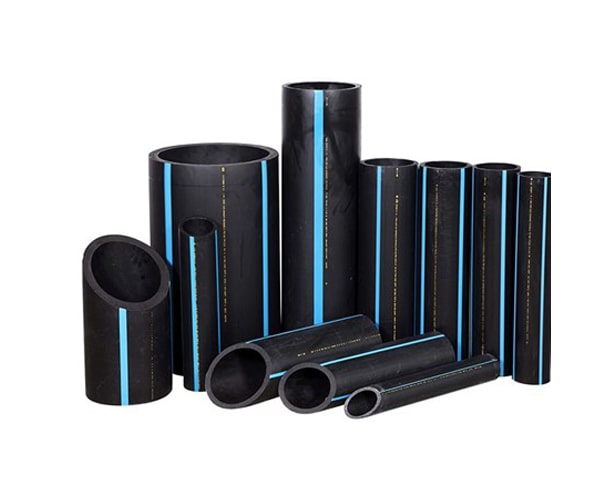
در ابتدایی ترین حالت، H1 یک فولاد ضد زنگ آستنیتی است. فولادهای زنگ نزن آستنیتی تقریباً به اندازه خود فولاد ضد زنگ هستند که توسط متالورژیست های آلمانی در دوره زمانی تقریبی 1909-1912 ساخته شده اند. آنها روی فولادهای 18 درصد کروم، 8 درصد نیکل کار کردند که کاملاً شبیه فولادهای زنگ نزن آستنیتی معمولی مانند 301، 302 و 304 هستند.
فولادهای “آستنیتی” به این دلیل نامیده می شوند چرا که این فولاد در دمای اتاق به جای فازهای معمولی فریت یا مارتنزیت در دمای اتاق در فاز “آستنیت” قرار دارد. اکثر فولادها اگر تا دمای کافی بالا (مانند 1340-1600 درجه فارنهایت) گرم شوند به آستنیت تبدیل می شوند. آستنیت به آرایش اتم های آهن در داخل فولاد اشاره دارد. بنابراین وقتی فولاد تا دمای بالا گرم می شود، به طور خود به خود از یک آرایش اتمی، فریت، با آرایش اتمی «مکعب مرکزی » به آستنیت تبدیل می شود، که آرایش «مکعبی در مرکز صورت» است. در اینجا نمایش شماتیک دو آرایش اتمی مختلف وجود دارد:
“سلول واحد” فریت مکعبی در مرکز. یک سلول واحد کوچکترین نمایش ممکن از ساختار بلوری است
سلول واحد در یک نمای بزرگتر از ساختار مرکزی فریت چگونه به نظر می رسد.
سلول واحد مکعبی آستنیت در مرکز صورت
نمای بزرگتر از آستنیت مکعبی در مرکز صورت
ساختار بلوری دقیق فریت و آستنیت به اندازه خواص آن مهم نیست. آستنیت به راحتی از فریت و مارتنزیت متمایز می شود زیرا غیر مغناطیسی است. بسیاری از چاقوسازان هنگام عملیات حرارتی از آهنربا استفاده می کنند تا بدانند چه زمانی فولاد به آستنیت تبدیل شده است. با این حال، فولادهای زنگ نزن آستنیتی به گونه ای طراحی شده اند که در دمای اتاق آستنیت باشند، بنابراین در دمای اتاق نیز غیر مغناطیسی هستند. روشی که آنها آستنیت را تا دمای اتاق تثبیت می کنند با افزودن عناصر آلیاژی مختلف است تا مارتنزیت در حین کوئنچ تشکیل نشود. معمولاً با فولاد چاقو تا دمای بالا گرم می شود تا آستنیت تشکیل شود و سپس خاموش می شود تا مارتنزیت سخت تشکیل شود. با این حال، عناصر آلیاژی مختلف دمایی را که در آن مارتنزیت تشکیل میشود، کاهش میدهند و میتوان آن را به زیر دمای اتاق کاهش داد:
Ms (°C) = 539 – 423*C – 311*N – 30.4*Mn – 17.1*Ni – 12.1*Cr – 7.5*Mo – 7.5*Si
در حالی که کربن بهترین عنصر برای کاهش دمای شروع مارتنزیت است، همچنین تمایل به تشکیل کاربید دارد. این بدان معناست که فولاد باید تا دمای بالاتر گرم شود تا همه کاربیدها حل شوند یا حتی تا جایی که کاربیدها بدون ذوب فولاد حل نشوند . کاربیدها همچنین اگر به اندازه کافی سریع سرد نشوند تمایل دارند در مرزهای دانه تشکیل شوند. به دلیل محتوای بالای کروم، فولادهای ضد زنگ با کربن در آنها تمایل به تشکیل کاربیدهای کروم دارند و تشکیل آن کاربیدها منجر به کاهش موضعی کروم در محلول می شود. اگر کروم یک کاربید تشکیل داده باشد، دیگر در محلول نیست تا به مقاومت در برابر خوردگی کمک کند. کروم باید در محلول باشد تا لایه غیرفعال تشکیل شود که از خوردگی جلوگیری کند. کروم بیشتر در محلول به معنای یک لایه غیرفعال قوی تر و مقاومت در برابر خوردگی بهتر است. بنابراین معمولاً از افزودن کربن در فولادهای زنگ نزن آستنیتی به دلیل پتانسیل کاهش مقاومت در برابر خوردگی اجتناب می شود.
کروم بالاتر مقاومت در برابر خوردگی را بهبود می بخشد و همچنین شروع مارتنزیت را کاهش می دهد، بنابراین افزودن کروم بیشتر راهی آسان برای ساخت فولاد زنگ نزن آستنیتی به نظر می رسد. با این حال، کروم همچنین یک “تثبیت کننده فریت” است. یک فاز فریت با دمای بالا به نام “دلتا فریت” وجود دارد که در نمودار زیر با رنگ آبی مشخص می باشد. دلتا فریت همان فریت معمولی با دمای پایین است اما در دماهای بالا یافت می شود.
نمودار فاز آهن-کربن 8% کروم که دلتا فریت (آبی)، آستنیت (قرمز) و فریت + آستنیت (بنفش) را نشان میدهد.
در بالا برای فولاد کروم 8 درصد است. فاز دلتا فریت در محدوده نسبتاً باریکی از دمای بسیار بالا برای فولاد کم کربن (~2350-2750 درجه فارنهایت) قرار دارد. در مقابل، میدان فاز آستنیت طیف وسیعی از دما و محتوای کربن را پوشش میدهد. میدان ارغوانی ترکیبی از فریت و آستنیت است. با این حال، افزودن کروم بیشتر، به دلیل اینکه تثبیت کننده فریت است، میدان فاز فریت دلتا را گسترش می دهد.
نمودار فاز 12% کروم آهن-کربن
با 12٪ کروم، میدان فاز دلتا فریت به شدت گسترش یافته است و میدان فریت + آستنیت به اندازه ای رسیده است که برای فولادهای بسیار کم کربن، میدان فاز قرمز کامل آستنیت در هر دمایی قابل دستیابی نیست. با وجود کروم بیشتر، میدان فاز آستنیت بسیار کوچک است:
نمودار فاز آهن-کربن 18% کروم
با 18٪ کروم، فاز آستنیت هرگز با فولاد بسیار کم کربن دیده نمی شود، و حتی فولادهایی تا حدود 0.5٪ کربن فقط می توانند تا حدی به آستنیت تبدیل شوند.
مولیبدن و سیلیکون نیز تثبیت کننده فریت هستند، بنابراین برای آستنیتی کردن فولاد نیز مفید نیستند. بنابراین معمولاً نیکل به فولادهای زنگ نزن آستنیتی و گاهی منگنز اضافه می شود، زیرا هم شروع مارتنزیت را کاهش می دهند و هم تثبیت کننده آستنیت هستند. در اینجا یک فولاد کروم 18٪ است که همچنین 8٪Ni اضافه شده است:
نمودار فاز آهن-کربن 18% Cr-8% Ni
پس از افزودن 8 درصد نیکل به فولاد 18 درصد کروم، میدان فاز فریت دلتا اکنون بسیار کوچک است و میدان فاز آستنیت بسیار بزرگتر است و به سمت محتوای کربن پایینتر تغییر میکند. بنابراین فولاد را می توان قبل از سرد شدن سریع به آستنیت گرم کرد تا آستنیت را در دمای اتاق حفظ کند.
خواص آستنیت و جایگزینی نیکل
فاز آستنیت به دلیل شکل پذیری و چقرمگی بسیار خوب آن مطلوب است. همچنین دارای استحکام تسلیم پایینی است که به این معنی است که عملیات شکل دهی روی فولاد آستنیتی نسبتاً آسان است. در برخی موارد خواص غیر مغناطیسی فولاد نیز مطلوب است. نیکل همچنین مقاومت در برابر خوردگی را با ترویج “عملکرد مجدد” هنگامی که لایه غیرفعال اکسید کروم از بین می رود، بهبود می بخشد. به ویژه در کاهش محیط و اسیدهای معدنی مفید است. نیتروژن همچنین Ms را کاهش می دهد و آستنیت را در دمای بالا تثبیت می کند، اما افزودن نیتروژن در مقادیر قابل توجهی دشوار است در حالی که نیتروژن کمتر از کربن نیترید کروم تشکیل می دهد، نیتروژن اضافی می تواند منجر به نیتریدها و کاهش مقاومت در برابر خوردگی شود. کاهش نیکل مطلوب است زیرا نیکل گران است. جایگزینی جزئی نیکل با منگنز در برخی گریدها استفاده می شود اما جایگزینی کامل عملی نیست. منگنز تقریباً نیمی از نیکل در گسترش میدان آستنیت مؤثر است و اثر اوج آن 5 درصد است و میدان آستنیت را با مقادیر بیشتر کوچک میکند بنابراین منگنز تنها می تواند جایگزین حدود 2.5٪ نیکل شود و منگنز مانند نیکل مقاومت در برابر خوردگی را بهبود نمی بخشد.
در واقع منگنز اثر منفی جزئی بر مقاومت در برابر خوردگی دارد. با این حال، برخلاف نیکل، منگنز حلالیت نیتروژن در فولاد مایع را بهبود می بخشد و بنابراین برخی از فولادها با ترکیبی از منگنز و نیتروژن برای جایگزینی نیکل تولید شده اند. بنابراین منگنز بالا در این فولادها در واقع به منظور افزودن نیتروژن بیشتر است و نه به دلیل خود منگنز.
تبدیل به مارتنزیت با کار سرد
هنگامی که فولادهای زنگ نزن آستنیتی تغییر شکل می دهند، در واقع مارتنزیت تشکیل می دهند، حتی اگر دمای شروع مارتنزیت کمتر از دمای اتاق باشد. مارتنزیت یک فاز بسیار قوی/سخت است که معمولاً فاز اولیه در فولادهای چاقو است. با نورد سرد، خمش، شکل دهی و غیره مارتنزیت در داخل آستنیت تشکیل می شود. در اینجا تصاویری از فولاد ضد زنگ 301 با افزایش سطوح “کرنش” وجود دارد که در آن می توانید صفحات مارتنزیتی را مشاهده کنید که با تغییر شکل فولاد شکل می گیرند:
فولاد ضد زنگ 301 با افزایش سطوح کرنش (درصد مشخص شده) نشان دهنده افزایش مارتنزیت است. تصاویر در حین کار سرد فولاد، نسلی از عیوب در سطح اتمی به نام “دررفتگی” وجود دارد. نابجایی در همه فلزات وجود دارد، اما چگالی نابجایی ها با مراحل مختلف پردازش و عملیات حرارتی متفاوت است. نابجایی ها فولاد را تقویت می کنند بنابراین هر چه کار سرد بیشتر باشد نابجایی های بیشتری وجود دارد و فولاد قوی تر می شود. استحکام فلزات با رفتار نابجایی ها کنترل می شود. در اینجا مثالی از افزایش سختی با کار سرد در فولاد ابزار حالت A8 آورده شده است:
این نابجاییهای سطح اتمی همچنین میتوانند به شکلگیری مارتنزیت از طریق “هستهزایی ناهمگن” کمک کنند. فازهای جدید تمایل دارند در مکان های مطلوب مانند کاربیدها، سطح فولاد یا مرز دانه ها شکل بگیرند. دررفتگی ها همچنین می توانند محل های مطلوبی برای تشکیل فاز جدید، در این مورد مارتنزیت باشند، بنابراین ایجاد تعداد بیشتری از آنها می تواند تشکیل مارتنزیت را تقویت کند. این مکانیسمی است که در آن تغییر شکل فولادهای آستنیتی منجر به تشکیل مارتنزیت می شود.
دمای پایین تر باعث تشکیل مارتنزیت در طول تغییر شکل می شود در حالی که دماهای بالاتر تشکیل مارتنزیت را به تاخیر می اندازد. آستنیت در دمای بالاتر پایدارتر است. شکل زیر میزان مارتنزیت تشکیل شده در مقابل مقدار کرنش در دماهای مختلف را نشان می دهد. در دمای 50-80 درجه سانتی گراد (125-175 درجه فارنهایت) تقریباً هیچ مارتنزیتی حتی با 60 درصد کرنش برای این فولاد خاص تشکیل نشد.
فولادهای زنگ نزن آستنیتی مختلف، بسته به ترکیب فولاد، کم و بیش مستعد تبدیل به مارتنزیت در طول تغییر شکل هستند. اثرات ترکیب تا حدودی متفاوت از آنهایی است که دمای شروع مارتنزیت را کنترل می کنند. یک معادله رایج پیشبینی دمایی است که در آن 50 درصد مارتنزیت با کرنش 30 درصد بر اساس ترکیب تشکیل میشود. بنابراین مقدار مارتنزیت تشکیل شده با کرنش برای یک دمای معین را می توان با M D30 بالاتر افزایش داد .
M D30 (°C) = 413 – 462*(C+N) – 9.2*Si – 8.1*Mn – 13.7*Cr – 9.5*Ni – 18.5*Mo
برخی از فولادها برای تقویت تشکیل مارتنزیت از طریق کاهش کربن (304L) یا با کاهش کروم و نیکل (301) طراحی شده اند. تشکیل مارتنزیت به این معنی است که از طریق نورد سرد فولاد می توان به استحکام بالایی دست یافت. ترکیب کار سرد برای افزایش استحکام از طریق تولید نابجایی ، و تشکیل مارتنزیت سخت به این معنی است که نورد سرد فولادهای زنگ نزن آستنیتی میتواند منجر به سطوح سختی نسبتاً بالایی شود، حداقل در مقایسه با فولادهای زنگ نزن آستنیت آنیل شده معمولی.
301 زنگ نزن با 90 درصد کاهش سرما حدود 55 Rcگزارش شده است که سختی مشابه فولادهای مارتنزیتی معمولی در چاقوهای مصرفی است، اگرچه کمتر از 60+Rc موجود در چاقوهای با کیفیت بالا است.
ترکیب فولاد H1
ترکیب H1 تفاوت زیادی با سایر فولادهای زنگ نزن آستنیتی مانند 301 و 302B ندارد.
فولاد 302B دارای یک Si بزرگ برای کمک به “مقاومت پوسته پوسته شدن” است، به این معنی که کمتر مستعد تشکیل رسوب در دمای بالا در حین آهنگری یا سایر عملیات است. Si در H1 ممکن است به همین دلیل به خوبی اضافه شود.
همچنین برای رسیدن به سختی بالا پس از نورد سرد طراحی شده است. سیلیکون یکی از بهترین ” تقویت کننده های محلول جامد ” است.
مولیبدن همچنین استحکام را افزایش می دهد، اما احتمالاً برای افزایش مقاومت در برابر خوردگی، به ویژه مقاومت در برابر حفره، به آن اضافه می شود. یک معادله رایج برای پیشبینی مقاومت حفرهای وجود دارد که در آن Mo تأثیر قویتری نسبت به کروم دارد. بنابراین Mo برای بهبود مقاومت در برابر خوردگی در محلول های کلریدی مانند آب نمک بسیار خوب است. نیتروژن همچنین مقاومت به خوردگی را بهبود می بخشد اما H1 مقدار بسیار کمی از آن را دارد. حال H1 را “فولاد نیتروژن” نمی نامیم زیرا بسیاری از فولادهای چاقو دارای مقدار مشابهی ازت هستند. بسیاری از مشخصات فولاد زنگ نزن آستنیتی مانند H1 دارای حداکثر نیتروژن 0.1٪ هستند، بنابراین H1 در بین کلاس فولاد آن دارای حداکثر نیتروژن مشابه نیست.
PREN = Cr + 3.3*Mo + 16*N
نیکل نیز مانند 301 نسبت به 302 و 304 به 7 درصد کاهش می یابد که به تقویت تشکیل مارتنزیت کمک می کند. کروم نیز در مقایسه با آن فولادها به 15 درصد کاهش یافته است. که تا حدودی مقاومت در برابر خوردگی را کاهش می دهد، اما تشکیل مارتنزیت را در طول نورد سرد تقویت می کند.
مقالات پربازدید
- مبلمان شهری با اسکلت فولاد مهر سهند: هنر پایداری در فضای عمومی
- تخت بیمارستانی با اسکلت فولاد مهر سهند: جایی که ایمنی، بهداشت و دوام به هم میپیوندند
- قدرت در عمق: جکهای سقفی سلیمی ساخته شده از لوله فولاد مهر سهند، ستون فقرات ایمنی ساختوساز
- کیفیت جکهای سقفی سلیمی ساختمانی
- کیفیت جکهای ساختمانی ساختهشده از لولههای فولادی